Common Causes of Hydraulic System Failures and How to Prevent Them
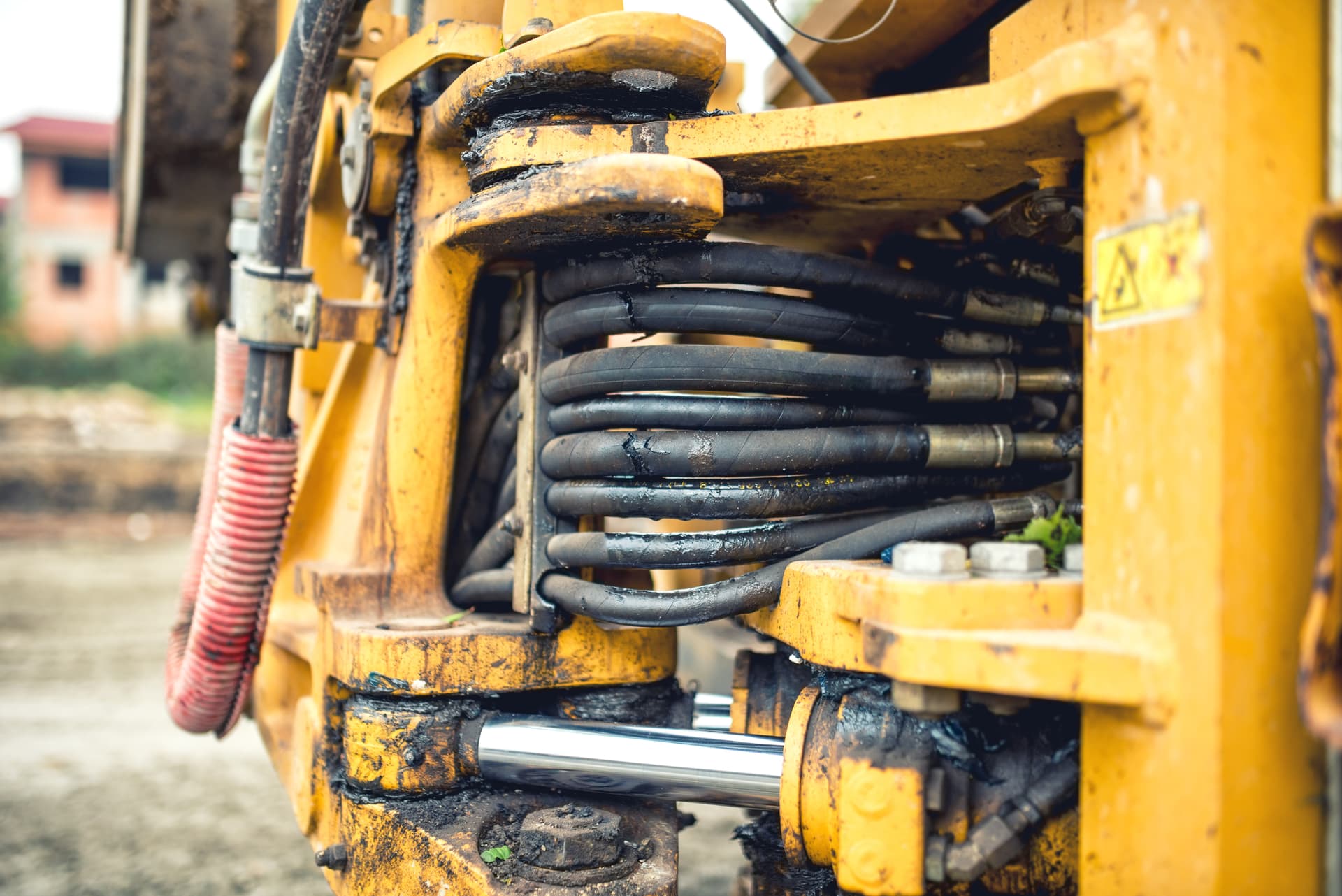
Introduction
Hydraulic systems are vital in numerous industrial applications, including manufacturing, construction, aerospace, and agriculture. However, these systems are susceptible to failures that can lead to costly downtime and repairs. Understanding the common causes of hydraulic system failures and how to prevent them can significantly enhance system reliability and efficiency. Below are the most frequent issues and their preventive measures.
Contamination
Hydraulic fluid contamination is one of the leading causes of system failure. Contaminants such as dirt, water, and metal particles can enter the system through various means, including during maintenance, through worn seals, or from inadequate filtration. Contaminated fluid can lead to abrasive wear, corrosion, and reduced efficiency of the hydraulic components. To prevent contamination, it is crucial to use high-quality filters and replace them regularly to remove contaminants from the hydraulic fluid. Ensuring that seals and gaskets are in good condition is also essential to prevent contaminants from entering the system. Additionally, maintaining a clean environment during maintenance or repairs can help avoid introducing contaminants into the hydraulic system.
Overheating
Overheating occurs when the hydraulic fluid temperature exceeds the optimal operating range, leading to fluid degradation, reduced lubrication, and increased wear on components. Overheating can result from high ambient temperatures, excessive load, or inadequate cooling. To prevent overheating, installing heat exchangers or coolers can help dissipate excess heat from the hydraulic fluid. Maintaining proper fluid levels is also important to ensure adequate heat dissipation. Additionally, monitoring and controlling the ambient temperature around the hydraulic system can help prevent overheating.
Fluid Leaks
Fluid leaks are a common issue in hydraulic systems and can occur due to worn seals, loose fittings, or damaged hoses. Leaks not only reduce system efficiency but can also pose safety hazards. Regular inspections are essential to identify and address leaks promptly. Using high-quality hoses, fittings, and seals can minimize the risk of leaks. Proper installation is also crucial to ensure that all components are correctly installed and tightened to the recommended specifications.
Aeration and Cavitation
Aeration occurs when air bubbles enter the hydraulic fluid, while cavitation happens when vapor bubbles form in the fluid due to low pressure. Both issues can cause noise, reduced efficiency, and damage to components. To prevent aeration and cavitation, maintaining adequate fluid levels is essential to prevent air from entering the system. Properly bleeding the hydraulic system can remove trapped air. Ensuring that pressure settings are within the recommended range can also help avoid cavitation.
Incorrect Fluid Selection
Using the wrong type of hydraulic fluid can lead to inadequate lubrication, increased wear, and compatibility issues with system components. It is important to always use hydraulic fluids recommended by the system manufacturer. Selecting fluids with the appropriate viscosity, thermal stability, and additive package for the specific application is also crucial. Regular testing of the hydraulic fluid can ensure it meets the required specifications.
Component Wear and Tear
Over time, hydraulic components such as pumps, valves, and cylinders can wear out due to friction, pressure, and operational cycles. Regular maintenance and timely replacement of worn components are essential to prevent failures. Ensuring proper lubrication of moving parts can reduce friction and wear. Using condition monitoring techniques can help detect early signs of wear and allow for corrective action before a failure occurs.
Improper Installation and Assembly
Incorrect installation or assembly of hydraulic components can lead to misalignment, excessive stress, and eventual failure. Ensuring that personnel are adequately trained in hydraulic system installation and maintenance is crucial. Following the manufacturer's guidelines and specifications for component installation and assembly can prevent issues related to improper installation. Using alignment tools and techniques can ensure components are properly aligned during installation.
Conclusion
Preventing hydraulic system failures requires a proactive approach, including regular maintenance, proper component selection, and adherence to manufacturer guidelines. By understanding and addressing the common causes of hydraulic system failures, you can enhance the reliability, efficiency, and lifespan of your hydraulic systems, minimizing downtime and reducing maintenance costs.