Pressure Perfect: A Comprehensive Look at Hydraulic Presses
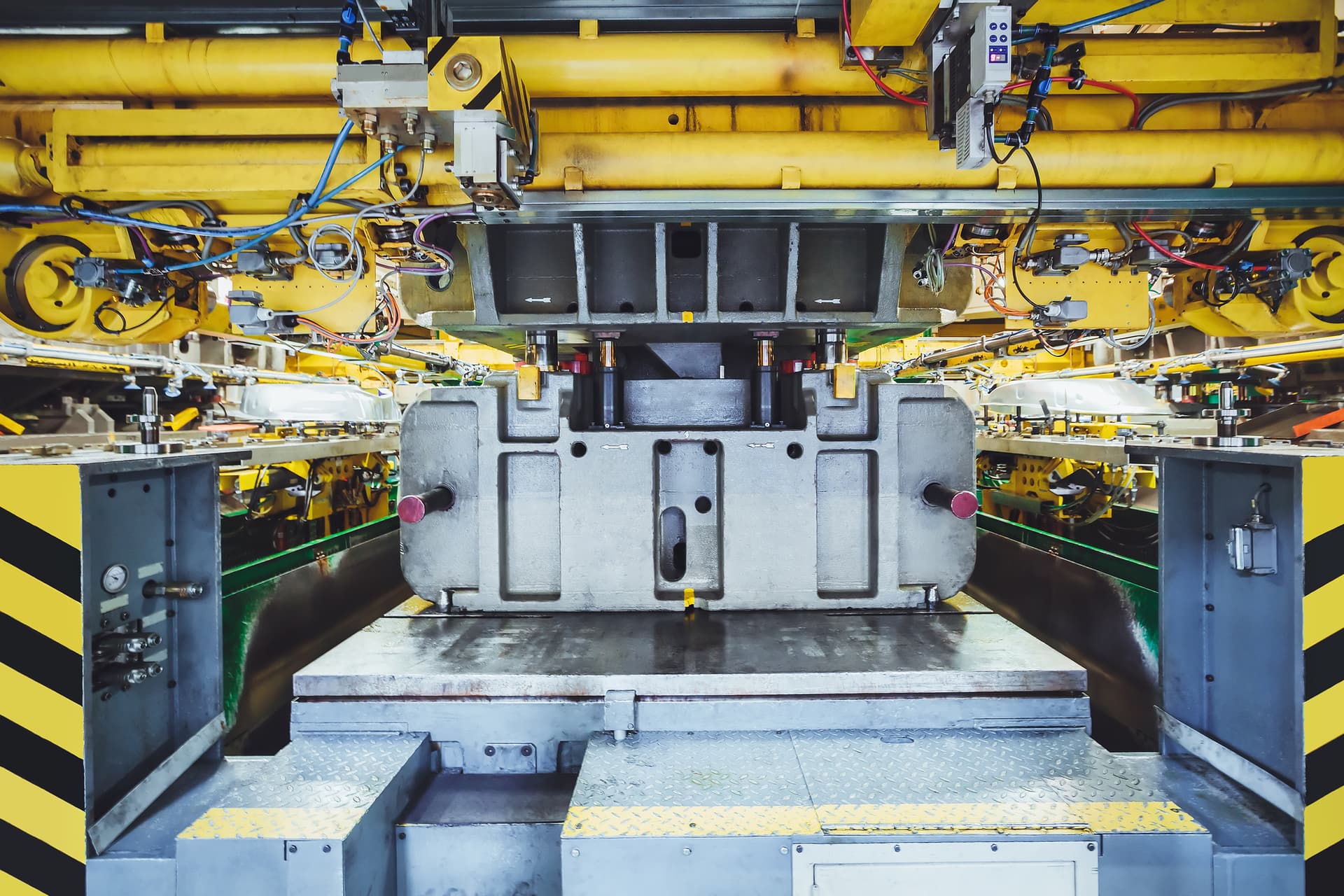
What are Hydraulic Presses?
Hydraulic presses are machines that use hydraulic fluid pressure to generate a compressive force. They operate based on Pascal's principle, which states that pressure applied to a confined fluid is transmitted equally in all directions. This principle allows hydraulic presses to exert significant force with minimal input, making them highly efficient and versatile tools in various industries.
Different Types of Hydraulic Presses
1. H-Frame Presses: Named for their H-shaped frame, these presses are versatile and widely used. They are ideal for bending, pressing, and straightening metal parts, as well as removing and installing bearings and bushings.
2. C-Frame Presses: These presses have a C-shaped frame, providing easy access to the working area from three sides. They are commonly used for tasks that require quick setups and frequent changes, such as assembly operations, punching, and riveting.
3. Four-Column Presses: Featuring four vertical columns, these presses offer exceptional stability and uniform pressure distribution. They are suitable for large-scale production, such as forming, molding, and deep drawing processes.
4. Bench Presses: Compact and designed to sit on a workbench, these presses are ideal for small-scale and precision work. They are used for tasks like jewelry making, small part assembly, and light-duty pressing applications.
5. Arbor Presses: Hand-operated presses used for light-duty tasks that require precise control. They are commonly employed for pressing, staking, and broaching small parts.
Uses of Hydraulic Presses
Hydraulic presses are incredibly versatile and find applications in various industries. In metalworking, they are used for forming processes like bending, drawing, and stamping, as well as cutting tasks such as shearing and blanking metal sheets. In the automotive industry, they are employed for assembly tasks, such as pressing bearings and bushings into place, and for maintenance tasks like straightening bent parts. In manufacturing, hydraulic presses are essential for molding plastic, rubber, and composite parts through compression molding, and for shaping metals in forging processes. In the construction industry, they are used for manufacturing concrete blocks, tiles, and other precast products, as well as for compacting materials to improve density and strength. In electronics, hydraulic presses are used for pressing electronic components into place on circuit boards and assemblies.
How to Maintain Hydraulic Presses
Proper maintenance is crucial to ensure the longevity and optimal performance of hydraulic presses. Regular inspections are necessary to identify signs of wear, leaks, or damage. This includes checking hoses, seals, and connections, as well as ensuring that pressure gauges are functioning correctly. Fluid maintenance involves regularly checking the hydraulic fluid level, using the recommended type and grade of hydraulic fluid, and monitoring the fluid's condition to replace it periodically. Lubrication of all moving parts, such as pivot points and bearings, as well as guides and rails, is essential to reduce friction and wear. Hydraulic filters should be replaced at regular intervals to prevent contaminants from entering the system. Frame alignment should be checked regularly to ensure even pressure distribution and prevent undue stress on components. Operational tests, including load testing and checking safety features like emergency stops and pressure relief valves, should be performed periodically to ensure the press can handle specified loads and that safety mechanisms are functioning correctly.