The Impact of Fluid Contamination on Hydraulic Systems
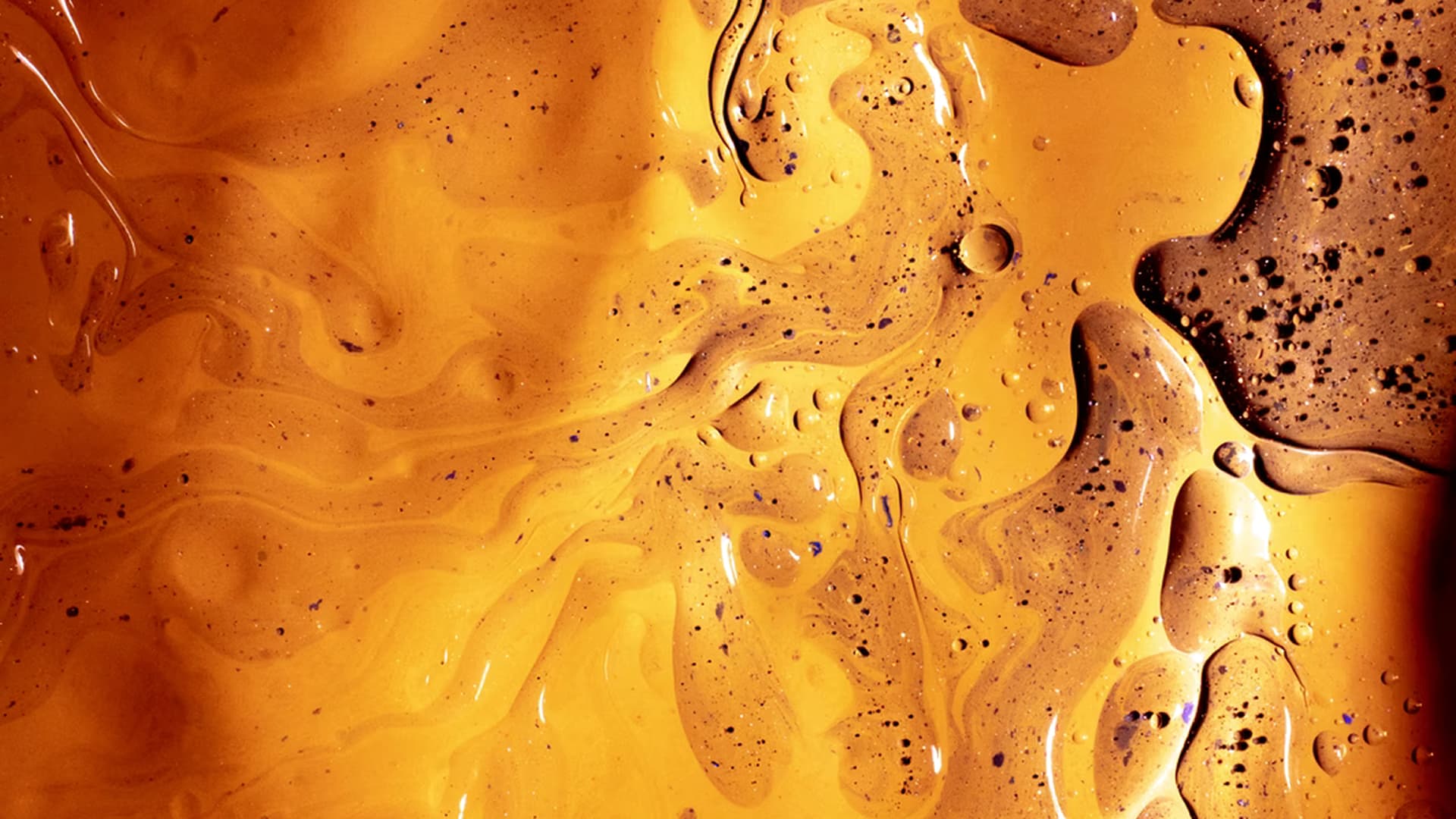
What is Fluid Contamination?
In this article, we will delve into the causes, effects, and preventive measures for fluid contamination in hydraulic systems. Fluid contamination refers to the presence of unwanted particles or substances in the hydraulic fluid. These contaminants can be solid particles, water, air, or chemical impurities that degrade the fluid's quality and compromise the system's functionality.
Common Sources of Contamination
1. Manufacturing Residue: New hydraulic systems or components often contain residual particles from manufacturing processes.
2. External Environment: Dust, dirt, and debris can enter the system through seals, vents, or during maintenance.
3. Wear and Tear: Internal components such as pumps, valves, and cylinders wear out over time, generating metal particles.
4. Fluid Degradation: Hydraulic fluid can degrade due to thermal stress, oxidation, or chemical reactions, producing harmful by-products.
5. Water Ingress: Moisture can enter the system through condensation, leaks, or contaminated fluid, leading to rust and corrosion.
Effects of Fluid Contamination
1. Reduced Efficiency: Contaminants increase friction and resistance within the system, reducing overall efficiency.
2. Component Wear: Abrasive particles cause accelerated wear of components, leading to premature failure.
3. Clogging and Blockages: Contaminants can clog filters, valves, and orifices, disrupting fluid flow and causing malfunctions.
4. Increased Heat: Contaminated fluid can cause overheating, which further degrades the fluid and components.
5. System Failures: Severe contamination can lead to catastrophic failures, resulting in costly downtime and repairs.
Detecting Contamination
1. Fluid Analysis: Regular sampling and analysis of hydraulic fluid can identify the presence and type of contaminants.
2. Filter Inspection: Checking filters for debris can indicate the level of contamination within the system.
3. Monitoring Performance: Unusual noises, vibrations, or drops in performance can signal contamination issues.
Preventive Measures
1. Proper Sealing: Ensure all seals and gaskets are in good condition to prevent ingress of contaminants.
2. Quality Fluid: Use high-quality, clean hydraulic fluid and store it properly to avoid contamination.
3. Regular Maintenance: Implement a routine maintenance schedule to inspect and replace filters, seals, and other components.
4. Filtration Systems: Install high-efficiency filtration systems to continuously remove contaminants from the fluid.
5. Training and Awareness: Educate personnel on the importance of contamination control and proper maintenance procedures.
6. Quality Adapters and Fittings: Use high-quality hydraulic adapters and fittings to ensure tight, leak-free connections and reduce the risk of contamination ingress.
Conclusion
Fluid contamination is a significant threat to the performance and lifespan of hydraulic systems. By understanding its sources, effects, and preventive measures, you can ensure your hydraulic systems operate efficiently and reliably. Regular maintenance, quality control, and proactive contamination management are key to protecting your investment and maintaining operational excellence. Remember, clean fluid is the lifeblood of a healthy hydraulic system.